Optimierung der Produktionseffizienz mit vorausschauender Wartung
In der sich rasch entwickelnden Welt der Fertigung ist Effizienz ein ständiges Thema. Die Unternehmen sind ständig auf der Suche nach neuen Methoden und Strategien zur Steigerung der Effizienz, da dies zu Umsatzeinbussen und Ressourcenverschwendung führt. Anlagenausfälle und ungeplante Stillstände sind die Hauptursachen für diese Ineffizienzen, die sich negativ auf die Produktivität und die Umsatzströme von Fertigungsunternehmen auswirken. Da die herkömmliche reaktive Wartung zu längeren Ausfallzeiten führt und die vorbeugende Instandhaltung nur oberflächliche Probleme erkennen kann, wenden sich die führenden Unternehmen der Branche der vorausschauenden Wartung zu, um die Effizienz von Produktionsanlagen das ganze Jahr über zu erhalten.
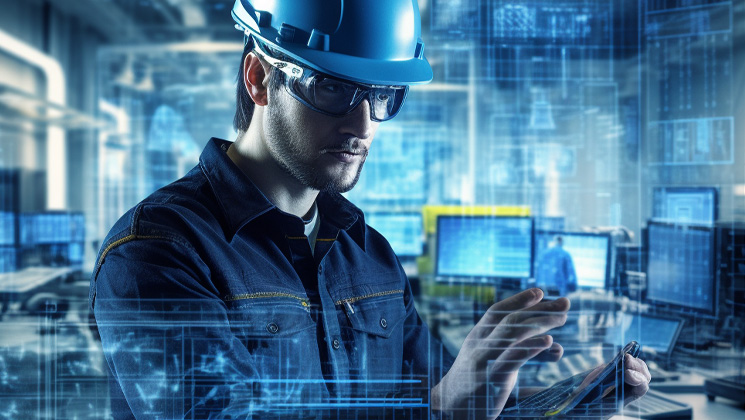
Vorausschauende Wartung: überblick, vorteile und nachteile
Die vorausschauende Instandhaltung (Predictive Maintenance, PdM) ist ein datengesteuerter Ansatz, der die ständige Überwachung der Leistung und des Zustands von Anlagen nutzt, um die besten Zeitpunkte für die Planung von Wartungsmassnahmen vorherzusagen. Die vorausschauende Instandhaltung zielt darauf ab, die Zeit bis zum Ausfall abzuschätzen, um die frühzeitigePlanung von Abhilfemassnahmen zu ermöglichen und so die Lebensdauer und Zuverlässigkeit der Anlagen zu maximieren. Diese Technik, die dank neuer Technologien immer ausgefeilter wird, umfasst im Wesentlichen die folgenden Komponenten: Datenerfassung, -verarbeitung und -analyse, Zustandsüberwachung, Vorhersage der Zeit bis zum Ausfall und Wartungsplanung.
Die Einführung der vorausschauenden Instandhaltung bringt mehrere Vorteile mit sich, von denen der erste die Steigerung der Produktionseffizienz ist. Nach Angaben von McKinsey and Company führt PdM zu einer Steigerung der Wartungseffizienz um 20%. Außerdem werden ungeplante Ausfallzeiten reduziert, die laut der Aberdeen Group bis zu 260.000 Dollar pro Stunde kosten. Es sorgt also für Kosteneinsparungen, die bei regelmäßiger, regelbasierter Wartung anfallen, und gewährleistet gleichzeitig die Maximierung des Lebenszeitwerts der Anlagen. Der Gesamteffekt ist eine Steigerung der Rentabilität und des Umsatzes für das Unternehmen.
Ein Argument gegen die vorausschauende Instandhaltung ist vielleicht die Komplexität, die mit dem Implementierungsprozess verbunden ist. Ein voll funktionsfähiges PdM-Programm erfordert ein hochqualifiziertes Team, um den Übergang vom vorherigen System zu der fortschrittlichen Software und Hardware zu erleichtern, die für die Zustandsüberwachung und Datenanalyse erforderlich ist. Dieser Prozess kann jedoch durch eine strategische Planung vereinfacht werden, bei der das Implementierungsprogramm zur leichteren Durchführung in Phasen unterteilt wird.
Rolle der Datenanalyse bei der Vorausschauenden Wartung
Daten sind für die vorausschauende Wartung von zentraler Bedeutung, und zu den Datentypen gehören in der Regel Sensordaten, historische Wartungsaufzeichnungen und Umgebungsdaten. Technologien wie Akustik, Vibrationsanalyse, Infrarot-Thermografie, Schallpegelmessungen und Koronadetektion erzeugen Sensordaten, die den Experten Aufschluss über den allgemeinen Zustand der Maschinen geben. Historische Wartungsprotokolle und die allgemeine Wartungshistorie bieten Einblicke in frühere Fehleranalysen, die ermöglichen Lebensdauer und Leistungstrends der Geräte abzuschätzen und so eine umfassendere Perspektive bringen. Und schliesslich überwachen Umgebungsdaten die äusseren Bedingungen - Temperatur, Luftfeuchtigkeit, Luftqualität -, die sich auf die Funktion der Geräte auswirken können.
Die Datenanalyse ist der nächste Schritt nach der Erfassung der Sensor-, historischen und Umweltdaten. Es gibt zwei Hauptmethoden der Datenanalyse in einem PdM-Programm: statistische Analyse und künstliche Intelligenz.
Die statistische Analyse verwendet mathematische Modelle, um Daten zu verarbeiten und Schlussfolgerungen zu ziehen. Anschliessend werden regelbasierte Modelle zur Vorbeugung von Geräteausfällen entwickelt. Die Analyse kann zum Beispiel ergeben, dass eine Maschine bei bestimmten Temperaturen ausfällt, woraufhin das Personal ein regelbasiertes System entwickelt, das einen Alarm auslöst, bevor dieser Temperaturpunkt erreicht wird.
Eine wesentliche Einschränkung der statistischen Analyse ist jedoch die Erstellung von Vorhersagen. Ausserdem ist es oft schwierig, Daten in einem breiteren Kontext zu betrachten, da diese Methoden in der Regel verschiedene Parameter isoliert betrachten.
Künstliche Intelligenz und maschinelles Lernen gleichen diese Einschränkungen aus, indem sie robuste Algorithmen einführen, die aus Daten lernen und Muster erkennen, die den meisten menschlichen Analysten entgehen würden, indem sie Techniken wie Support-Vektor-Maschinen und neuronale Netze einsetzen. Daher können sie für Vorhersagen mit einem hohen Mass an Sicherheit verwendet werden. Im Gegensatz zu statistischen Modellen, die Parameter isoliert betrachten, wird beim maschinellen Lernen ein umfassenderer Ansatz verfolgt, bei dem alle Eingaben gleichzeitig berücksichtigt werden. Folgerichtig steht das maschinelle Lernen heute an der Spitze der Datenanalyse in der vorausschauenden Instandhaltung, und es bringt den Unternehmen, die es einsetzen, weiterhin spannende Erträge.
5 Herausforderungen, Denen sich Hersteller bei der Einführung der Vorausschauenden Wartung Gegenübersehen Können
Obwohl die Ergebnisse lohnend sind, kann der Prozess der Einführung einer vorausschauenden Instandhaltung eine Herausforderung sein. Fertigungsunternehmen, die eine Umstellung ihrer bevorzugten Wartungsmethode auf eine vorausschauende Methode planen, müssen sich darüber im Klaren sein, was es bedeutet, ein erfolgreiches Programm einzuführen und aufrechtzuerhalten.
Hier sind die 5 grössten Herausforderungen, mit denen Sie rechnen müssen, wenn Sie die Einführung der vorausschauenden Wartung in Ihrem Unternehmen in Erwägung ziehen:
1. Datenqualität
Der Unterschied zwischen Erfolg und Misserfolg eines PdM-Programms liegt in der Qualität der zur Verfügung gestellten Daten. Qualitativ hochwertige und genaue Daten sind notwendig, damit das Programm seine Ziele erreichen kann. Daher müssen die Unternehmen von Anfang an viel Arbeit in die Validierung aller Datenquellen investieren.
2. Datenintegration und -standardisierung
Es ist wichtig, Daten aus unabhängigen Quellen zusammenzutragen und dann die Informationen zu standardisieren, um eine einheitliche Sicht auf den Zustand der Ausrüstung zu erhalten. Die damit verbundenen Prozesse sind oft komplex und zeitaufwändig, da die Daten wahrscheinlich über zahlreiche Quellen verstreut sind und in verschiedenen Formaten und Strukturen vorliegen.
3. Kosten
Die Einführung eines vorausschauenden Wartungssystems erfordert hohe Vorlaufkosten. Die Fertigungsunternehmen müssen die für die Datenerfassung und -verarbeitung erforderliche Hardware und Software bezahlen. Auch für das Personal zur Überwachung des Programms müssen zusätzliche Mittel bereitgestellt werden.
4. Technisches Fachwissen
Jedes Programm zur vorausschauenden Wartung benötigt Experten wie Datenanalysten, Datenwissenschaftler und Experten für maschinelles Lernen. Solche Fachleute sind sehr gefragt und knapp, was ihre Einstellung zu einer echten Herausforderung macht.
5. Adoption
Die Umstellung von reaktiver oder präventiver Instandhaltung auf PdM ist für ein Unternehmen und sein Personal eine bedeutende Veränderung. Infolgedessen können einige Beteiligte zögern, diesen neuen Instandhaltungsprozess anzunehmen, was den Umsetzungsprozess erheblich verlangsamt.
Umsetzung in der Praxis - Eine Fallstudie aus der Fertigung
Zahlreiche Unternehmen des verarbeitenden Gewerbes haben ein vorausschauendes Wartungsprogramm eingeführt und damit bemerkenswerte Ergebnisse erzielt. Ein gutes Beispiel ist Duke Energy, eines der grössten Energieunternehmen in den Vereinigten Staaten. Nach einem katastrophalen Ausfall, der 10 Millionen US-Dollar an Bussgeldern und erhebliche Umsatzeinbussen kostete, startete das Unternehmen sein SmartGen-Programm. Die SmartGen-Initiative stützte sich auf das industrielle Internet der Dinge (IIoT) und Big-Data-Analysen zur Zustandsüberwachung und vorausschauenden Wartung. Das Programm war erfolgreich und Duke Energy sparte innerhalb der ersten drei Jahre 31,5 Millionen US-Dollar an Reparaturkosten ein.
In ähnlicher Weise hat die BMW Group ein PdM-Programm eingeführt, das Sensoren, Datenanalyse und künstliche Intelligenz einsetzt, um ein System zur Wartung ihrer Maschinen zu entwickeln. Die Anwendungen des BMW-Systems sind vielfältig. So wird es beispielsweise in der Fahrzeugmontage eingesetzt, um Stillstandzeiten bei Förderbändern zu vermeiden, und in Karosseriewerkstätten, um sicherzustellen, dass die Schweisszangen funktionsfähig bleiben. Die Mitarbeiter werden durch visuelle Warnungen und Hinweise darauf aufmerksam gemacht, dass die Wartung der Anlagen fällig ist. Noch nachhaltiger wird das Programm von BMW durch seine cloudbasierte Plattform, die einen nahtlosen Datenaustausch innerhalb des gesamten globalen BMW Group Netzwerks ermöglicht. Da BMW die vorausschauende Wartung auf so hohem Niveau durchführt, kann das Unternehmen nun die Produktionseffizienz aufrechterhalten und die Rentabilität sicherstellen.
Diese Fallstudien sind nur zwei von vielen, die den Wert der vorausschauenden Instandhaltung in der Fertigungsindustrie verdeutlichen.
Die Zukunft der Vorausschauenden Wartung und Datenanalyse
Im Zeitalter von Industrie-4.0-Technologien wie künstlicher Intelligenz, maschinellem Lernen, dem industriellen Internet der Dinge (IIoT), Big-Data-Analysen und Automatisierung ist die Zukunft der vorausschauenden Wartung vielversprechend. Nach Angaben des Weltwirtschaftsforums wird die Einführung dieser Technologien bis 2030 zu einer Steigerung der weltweiten Fertigungsproduktivität um 15-20 % führen.
KI und maschinelles Lernen sind in der Lage, fortschrittliche prädiktive Analysen durchzuführen, die die Genauigkeit und Skalierbarkeit für Unternehmen verbessern werden. Das IIoT bietet nahtlose Konnektivität zwischen Hardware und Software und gewährleistet einen schnellen Datenaustausch zwischen Maschinen und menschlichen Bedienern. Dies bedeutet, dass PdM auf einem höheren Niveau als je zuvor implementiert werden kann, was die Rentabilität für Hersteller erhöht. Und schliesslich bedeutet das Aufkommen von Cloud Computing, dass Hersteller weiterhin mehr Daten für die Analyse sammeln können, ohne durch geringe Speicherkapazitäten eingeschränkt zu sein.
Schlussfolgerung
Die Minimierung von Ausfallzeiten und die Maximierung der Lebensdauer von Anlagen ist der Schlüssel zur Optimierung der Produktionseffizienz und der Umsatzgenerierung. Die vorausschauende Instandhaltung ist eine Strategie, die umfassende Lösungen für die Herausforderungen bietet, mit denen Hersteller konfrontiert sind. Es handelt sich um einen datenintensiven Ansatz, aber die Verfügbarkeit von künstlicher Intelligenz, Cloud Computing und Industrial Internet of Things (IIoT) vereinfacht den Prozess für Unternehmen, die diese Lösung implementieren möchten, erheblich.
Wir von ACTUM Digital liefern das letzte Puzzleteil, indem wir Ihr Unternehmen bei der Einführung dieser neuen Technologien und der Entwicklung effektiver Datenstrategien unterstützen, damit Ihr PdM-Programm erfolgreich ist. Finden Sie hier heraus, wie wir Ihnen helfen können, Ihre Ziele für die Produktionseffizienz schneller und kostengünstiger zu erreichen.
Das könnte Ihnen auch gefallen...
[19/05/2023] Wie verändert Big Data Analytics die Fertigungs- und Lieferkette
Die Möglichkeiten der Big-Data-Analytik für die Optimierung der Lieferkette in der Fertigung sind unbegrenzt. Erfahren Sie, welche Implementierungsschritte Sie befolgen müssen, um die zahlreichen Vorteile dieser Technologie zu nutzen.
Lesen Sie den Insight